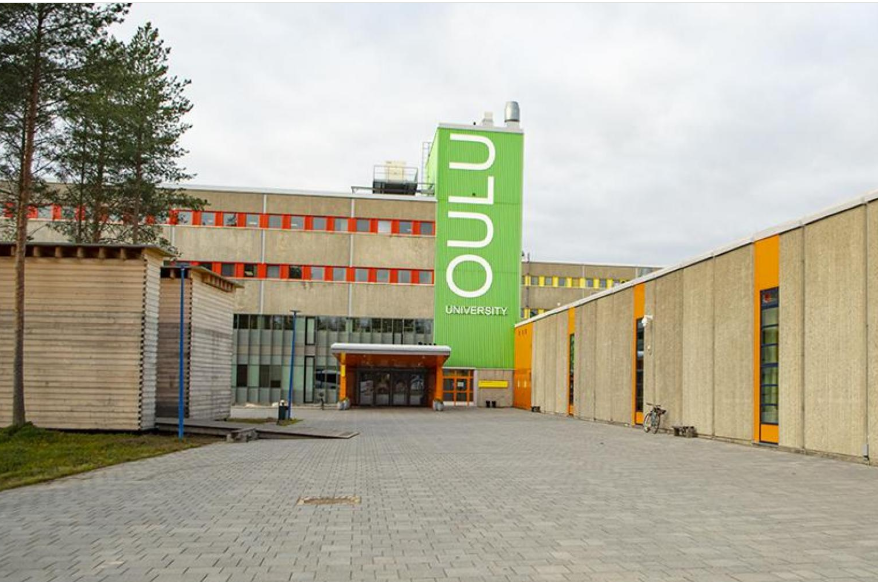
Steel remains an essential material, particularly in the construction and manufacturing sectors, due to its exceptional properties, such as adaptability and recyclability. The steelmaking industry contributes approximately 7% of carbon dioxide and consequently, much attention is given to the shift towards a cleaner alternative for sustainable production. The transition from fossil-based burner fuels to cleaner alternative fuels in steel billet and slab reheating will contribute to reducing GHG emission sources in steel manufacturing.
Assessment of the steel product quality
In attaining a transformative drive towards zero emission with GHG emission reduction associated with changes to the burner’s fuel and post-burn atmosphere in slab reheating, an important aspect to monitor and maintain is the quality of steel products.
In the TWINGHY project, OULU will research steel quality by investigating scale formation by substituting burners’ fossil fuel with incorporating hydrogen as a fuel and oxy-combustion in a reheating furnace. Variations in burner fuel and post-burn atmosphere can significantly influence the oxide scale, the formation rate, and the morphology of steel products during the reheating of the slabs. Additionally, changing to the burner’s fuel has the potential for greater oxidation, resulting in increased oxide formation and could pose significant challenges in managing oxide scales compared to current industrial practices.
The research will focus on factors such as holding time, the gas components in the atmosphere, and temperature inside a reheating furnace in assessing the impact of these parameters on the formation and growth of the oxide scale on the steel surface.
In collaboration with partners such as CELSA, OULU’s tasks in this project will be to conduct thermogravimetric tests and use characterisation techniques such as electron microscopy to study oxide scales obtained from a laboratory scale that simulate different furnace atmospheres. The research aims to assess the differences in oxide scale formation rates and morphologies on steel between current industrial heating practices and proposed improvements integrating hydrogen as a fuel and oxy-combustion.
A reference oxide scale formation database for selected steels will be developed based on the current practice of natural gas burning with air. A further dataset will be created that compares using different burner practices with the aims of GHG reductions from the reheating process regarding the amount of oxide scale with the reference case (natural gas burning with air). The results will assist in determining which steel types are most prone to see high changes to oxide formation during the switch to greener heating practices (furnace fuelled with hydrogen) will be formed.
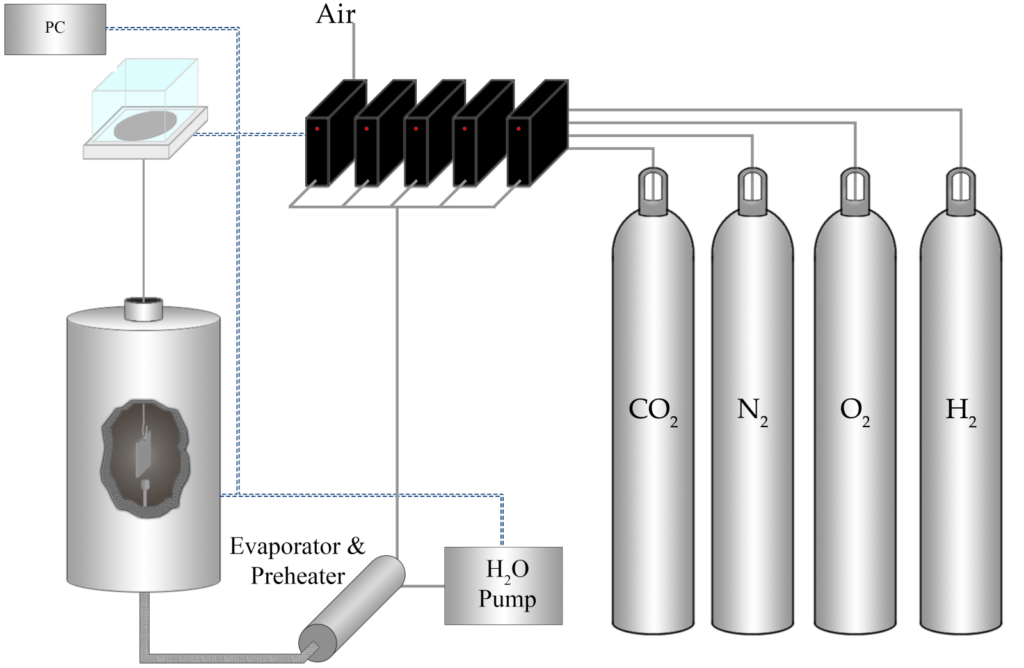
Author: Dr Francis Gyakwaa
Dr Francis Gyakwaa is a postdoctoral researcher with the process metallurgy research unit at the University of Oulu, Finland. His research interest is steel cleanliness and quality assessment, such as non-metallic inclusions, metallurgical slag and scale formation using various characterization techniques. Francis’s role in the TWINGHY project includes conducting thermogravimetric tests and utilizing characterization techniques for scale formation studies.