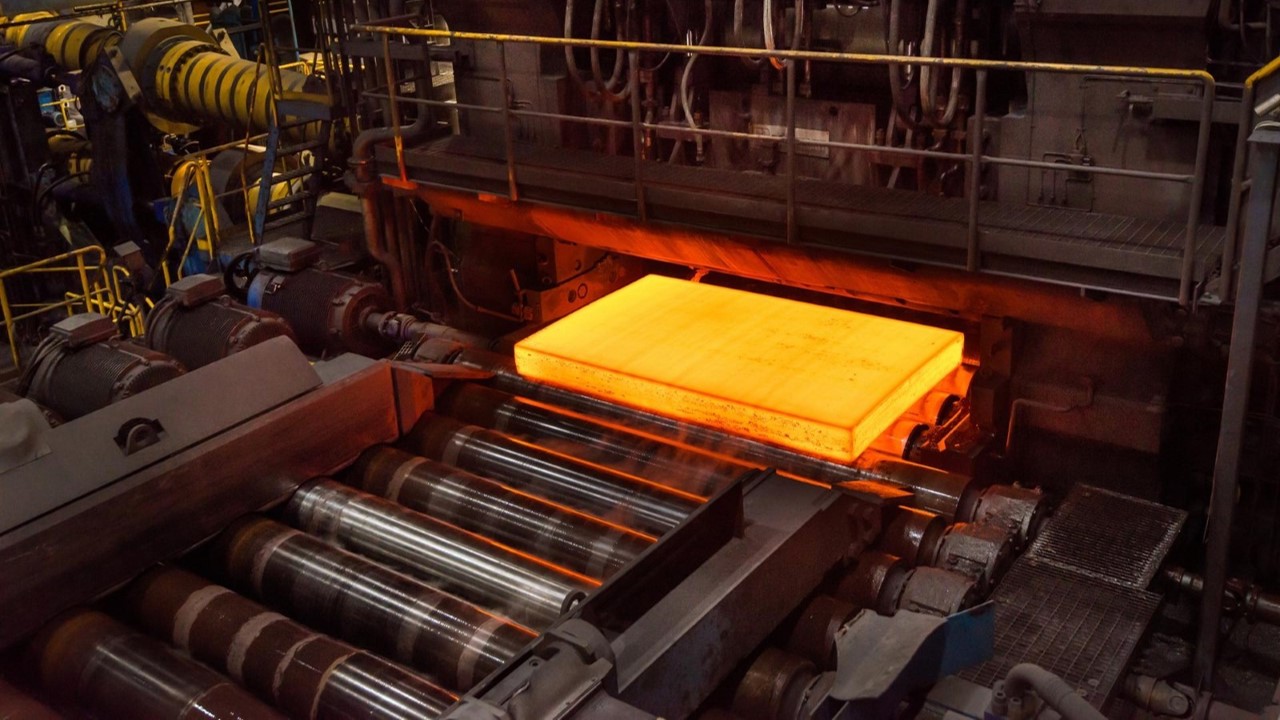
Our world is built using steel. Cars, trucks, houses, cranes and bridges are just a few examples of items where steel plays a decisive role. And if something is not made out of steel, it’s probably built with a machine made of steel.
Steel has many advantages and that’s why it’s used in every aspect of our lives. Recyclable, strong and durable are just a few of its many advantages. However, the steel industry remains a significant source of CO2 emissions and SSAB is fully committed to fight climate change.
With our steel solutions, we want to contribute to a sustainable society, revolutionize our industry and eliminate the CO2 emissions from steelmaking. Our ambition can reduce Sweden’s CO2 emissions by 10% and Finland’s by 7%, and lead the steel industry toward a greener future.
Innovation is our key to success
The key to SSAB’s success has always been our continuous ambition to develop, improve and innovate our steels and related services. We’re actively pushing for new and better solutions with our customers.
In TWINGHY, SSAB is reexamining the slab heating process in collaboration with other leading European steel makers. Traditionally, slab heating furnaces have been fueled by fossil fuels. Transitioning out of CO2 intensive fuels can be done by refurbishing furnaces to burn other fuels, such as LPG, biogas and hydrogen gas, with fuel flexibility in mind. We look forward to increased use of green hydrogen in industry. Through this project, we will gain both direct experience and work for how a better technical understanding of how conversion to hydrogen heating can be made, and the economic viability of such an investment.
SSAB is cooperating with SWERIM to model the heating process for better precision and lower energy consumption, using one of our slab reheating furnaces as basis.
We’re revolutionizing steelmaking
Resource scarcity, continuing urbanization and climate change, combined with the increasing need for new infrastructure, create a growing need for more sustainable solutions. We firmly believe that SSAB and steel are part of the solution.
We’ve already succeeded in producing the world’s first fossil-free steel based on fossil-free sponge iron and HYBRIT® technology, developed together with our partners LKAB (Europe’s largest iron ore producer) and Vattenfall (one of Europe’s largest energy producers).
HYBRIT® technology replaces coking coal, traditionally needed for ore-based steelmaking, with hydrogen. We’ve shown that the technology is possible and CO2 emissions can be virtually eliminated. The by-product is water.
We´ve delivered the first concept batches of fossil-free steel to key customers for production of, for example trucks, dumpers, car seats and watches. The next step is to ramp up this technology to an industrial scale and intensify our efforts to further reduce CO2 emissions throughout the production chain.
Authors: Carl Ellström, Jonas Engdahl
Carl Ellström is a process engineer at SSAB with a master’s degree in Engineering Physics from KTH in Stockholm. He has wide experience from the steel & energy industries, as well as academic research.
Jonas Engdahl is a senior specialist in heating technology at SSAB, holding a Master’s degree in Mechanical Engineering from NTNU in Trondheim, Norway. Throughout his career, he has worked in both practical roles and with R&D to develop solutions that enhance performance and minimize environmental impacts in steel processing.